Let’s consider a common industrial pressure transmitter used for measuring process pressure in a pipeline carrying a liquid or gas. Now it’s time to remove the pressure transmitter, then how should we do and what need to be careful?
Safety protocols
Before removing this transmitter from live service, it’s crucial to follow proper safety protocols to avoid potential hazards.
First, we need to isolate the transmitter from the process line by closing the root valve and the bypass valve. This step ensures that no process fluid can flow into the transmitter during removal. Next, we need to vent or drain any residual pressure or fluid trapped between the closed valves and the transmitter. This is done by carefully opening the vent or drain valve, allowing the trapped fluid or gas to escape safely.
Vent Fitting
Now, let’s talk about the vent fitting itself. Imagine a small valve or opening on the transmitter body, typically equipped with a small plug or cap. This fitting is designed to allow the equalization of pressure between the internal components of the transmitter and the atmosphere.
During normal operation, this vent fitting is left open to allow proper pressure measurement.
However, when removing the transmitter, we need to be cautious about this vent fitting. If it’s left open, any residual process fluid or gas could potentially leak out, creating a safety hazard or environmental concern. To prevent this, we need to carefully close or seal the vent fitting before completely removing the transmitter.
For instance, if the vent fitting has a small screw-on cap, we would gently tighten it to seal the opening. If it’s a small valve, we would turn it to the closed position. This step ensures that any remaining fluid or gas inside the transmitter is contained and cannot escape during removal and transportation.
Safety Instruction
It’s essential to follow the manufacturer’s specific instructions for sealing the vent fitting on that particular transmitter model. Additionally, we should wear appropriate personal protective equipment (PPE) such as safety glasses, gloves, and a face shield, as a precautionary measure against any potential leaks or exposure.
By isolating the transmitter, venting or draining any trapped fluid or gas, and carefully sealing the vent fitting, we can safely remove the pressure transmitter from live service while minimizing risks to personnel, equipment, and the environment.
What else should be noted
Before removing a pressure transmitter from live service, the technician must “bleed” or “vent” accumulated fluid pressure to atmosphere in order to achieve a zero energy state prior to disconnecting the transmitter from the impulse lines.
Some valve manifolds provide a bleed valve for doing just this, but many do not. An inexpensive and common accessory for pressure-sensing instruments (especially transmitters) is the bleed valve fitting or vent valve fitting, installed on the instrument as a discrete device.
The most common bleed fitting is equipped with 1/4 inch male NPT pipe threads, for installation into one of the 1/4 inch female NPT pipe ports typically provided on pressure transmitter flanges. The bleed fitting is operated with a small wrench, loosening a ball-tipped plug off its seat to allow process fluid to escape through a small vent hole in the side of the fitting.
The following photographs show close-up views of a bleed fitting both assembled (left) and with the plug fully extracted from the fitting (right). The bleed hole may be clearly seen in both photographs:
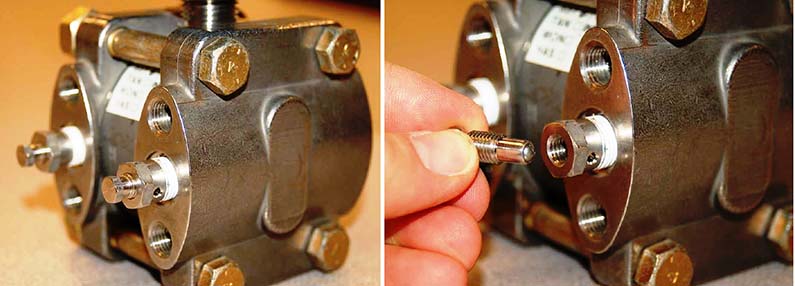
When installed directly on the flanges of a pressure instrument, these bleed valves may be used to bleed unwanted fluids from the pressure chambers, for example bleeding air bubbles from an instrument intended to sense water pressure, or bleeding condensed water out of an instrument intended to sense compressed air pressure.
The following photographs show bleed fittings installed two different ways on the side of a pressure transmitter flange, one way to bleed gas out of a liquid process (located on top) and the other way to bleed liquid out of a gas process (located on bottom):
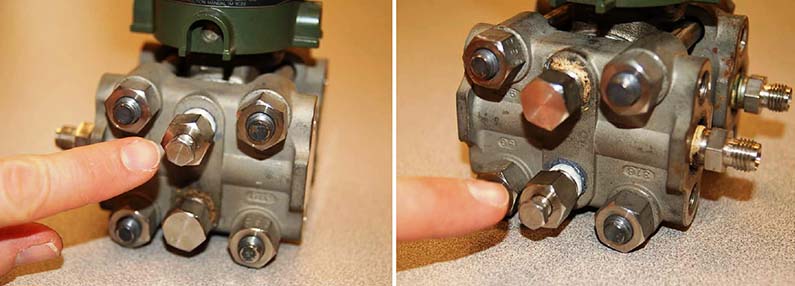
NOTE : The standard 3-valve manifold, for instance, does not provide a bleed valve – only block and equalizing valves.
With the bleed plug completely removed, the open bleed fitting provides a port through which one may apply air pressure for testing the response of the pressure transmitter.
A special test fitting called a bleed port adapter or DP transmitter calibration fitting – colloquially known as a stinger – threads into the opened bleed fitting.
Special fitting & Bleed port adapters
This special fitting allows a compression-style tube to be temporarily connected to the opened bleed port, which then allows the connection of an air pump and test pressure gauge to the transmitter. Thus, the bleed port adapter enables a technician to conveniently apply test pressures to the DP transmitter without having to loosen any of the instrument manifold bolts, tapered thread pipe connections, or impulse tube compression fittings.
When performing field checks of pressure transmitters, bleed port adapters substantially reduce the amount of time necessary to field-test pressure instruments. The following sequence of illustrations show how a bleed port adapter may be used in conjunction with a three-valve instrument manifold to isolate a DP transmitter from a process and then subject it to test pressures from a hand pump:
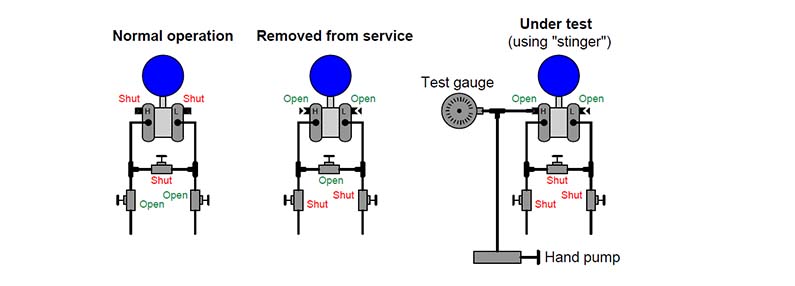
Note how both bleed vents must be opened, and the equalizing valve shut, in order to apply a test pressure to the DP transmitter.
Although it is possible to safely bleed pressure from both sides of a DP instrument through just one bleed fitting (through the open equalizing valve), both bleeds must be open in order to perform a pressure test. If the “L” side bleed fitting is left in the shut position, some pressure may be trapped there as pressure is applied to the “H” side by the hand pump. If the equalizing valve is left open, no difference of pressure will be allowed to form across the DP instrument.
Conclusion
Removing a pressure transmitter from live service requires careful planning and execution. First, isolate the transmitter by closing valves and venting or draining trapped fluid.
Carefully seal the vent fitting to contain any residual material. Verify safe operating conditions, perform leak tests, and address any issues before removal.
Follow manufacturer guidelines, use appropriate PPE, and comply with site safety protocols. Proper handling and containment during transportation are essential.